

Top 10: Worst supply chain disasters in history
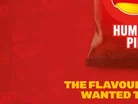
Walkers - the world’s largest single producer of crisps (or ‘potato chips’, if you’re from North America) - has taken out full-page adverts in national UK newspapers, to apologise for the ongoing shortage of its products.
The UK firm, based in Leicester, has been at the centre of a crisp-shortage storm for almost a month. Yet the problem has nothing to do with congested container ports, a lack of lorry drivers or any of the other multitude of pandemic-fuelled supply chain issues affecting so much of the world.
The problem was caused by a computer glitch, following an IT upgrade made by parent company, PepsiCo.
Following weeks of shortages, Walkers has now formally apologised to customers, across social media and also in full-page ads in national newspapers.
In the ad, headed ‘Humble Pie: the flavour we never wanted to taste’, Walkers says the situation is “getting better” and that it is “working 24/7 to address the backlog and meet orders”.
You have to feel for them. So, in order to make the C-suiters at Walkers feel a little better about things, here are ten wince-inducing examples of supply chain own-goals from history - some of which make Walkers’ problems seem minor by comparison.
10. KFC, 2018
Why didn't the chicken cross the road? Because of KFC’s supply chain and its lack of contingency planning. February 14, 2018 is not a day KFC UK will look back on with love hearts in its eyes. This was the day it moved to a new supply chain provider, switching from Bidvest to DHL. Bidvest had six warehouses, DHL had just one. That’s an important detail. That warehouse was in Rugby, smack-bang in the middle of the UK. That’s another. The same morning, a fatal traffic incident closed the M6 motorway near… Rugby. With its lorries stuck in the traffic - and no other locations from which to dispatch chicken - KFC was in big trouble. By February 18, just 266 of its 870 restaurants in the UK and Ireland were open. It was lampooned by the country's media for poor planning.
9. Denver International Airport, 1995
Following long delays, this brand-new airport finally opened in 1995. Early in the planning stage, United Airlines insisted on an ambitious automated high-speed baggage system that ran from the concourses to the main terminal. But technical and communication problems meant the system was only ever partly operational, and in aviation circles its mishandling of bags became the stuff of legend, with clothing and personal effects scattered beneath the system's tracks as luggage was spewed off. In the end, United returned to traditional handling methods.
8. Toys R Us, 1999
In September 2018 Toys R Us filed for bankruptcy but back in 1999 it was red hot. E-retail was really heating up, and the online division of Toys R Us advertised heavily. Santa-like, the company promised to fulfil Christmas deliveries on any order placed by December 10, and was duly swamped by tens of thousands of orders. Although most of its inventory was in place, it simply couldn’t pick, pack and ship the orders fast enough. Some employees worked 49 straight days to meet demand, but to no avail. Just days before Christmas, Toys R Us was less Santa, and more Grinch, as it sent out thousands of now-infamous, “We’re sorry,” emails, telling customers their orders would not be arriving in time for Christmas. Never have so many tears been shed by so many children in such little time.
7. Hershey, 1999
As for all chocolate makers, Halloween is a trick-or-treat cash-fest. It’s their sales sweet-spot. In 1999, Hershey spent more than $100 million on transforming its IT infrastructure and supply chain. Expected to go live in April, 1999, the schedule slipped, and rather than wait until the following year, Hershey switched over in the summer. But the system was dogged with issues, not least of which was that inventory was not visible to the order management system. As a result, $150 million in orders were missed. Quarterly profit dropped by 19 per cent and the company’s stock value plummeted.
6. Snap-on Tools, 1997
The US maker of high-end tools and equipment for use in the transportation industry installed an order management system implementation in 1997. It didn’t work, and led to $50 million in lost sales for the first half of 1998. Meanwhile, operating costs soared by 40 per cent, as extra staff were hired to overcome system issues. The company’s profits dropped by 22 per cent in 1998.
5. Adidas, 1996
In 1993, the German sports shoe-and-clothing maker implemented a warehouse management system in its Spartanburg distribution hub in South Carolina. But the IT firm it was using went bust mid-project, so it engaged another, and forged ahead. Frustrated by long delays, in 1996 Adidas went live before the system was ready. Nothing worked, and it was unable to process and ship orders. It was able to fulfil just one fifth of its $50 million orders in North America. Adidas suffered market-share losses for years after, and haemorrhaged IT and logistics staff.
4. Nike, 2001
In this year, sports-gear giant Nike went live with a new - and supremely complex - supply chain planning system. Bugs and integration left the company with significant inventory shortages and excesses. Nike ended up slashing prices to get rid of the additional inventory, putting pressure on margins and profits. At a quarterly conference call, Nike cited “software problems” for causing a $100 million revenue shortfall, and Wall Street knocked 20 per cent off its stock price.
3. Apple, 1995
Back in 1995, Apple was market leader in a deeply fragmented PC market. But that all changed, thanks to a supply chain blunder. That year, Apple was set to introduce its new line of PowerMac PCs just before the Christmas season. Having been burned two years earlier by excess inventory after aggressively launching its PowerBook laptops, the company throttled back on inventory. But demand for PowerMacs went stratospheric and Apple was left facing $1 billion in unfilled orders. Its stock price was slashed by half, and the company spiraled into a cycle of decline that only the return of its visionary founder, Steve Jobs, was able to arrest.
2. General Motors, 1980-85
For 20 years, GM was the world's most profitable company. By 1970 its revenue was $22.8 billion. Now, it’s an also-ran auto manufacturer, and the seeds of its decline can be traced back to its desire to automate its supply chain. Reacting to a 1970s labour strike, then-CEO Roger Smith vowed to roboticise the manufacturing process. Between 1980 and 1985 the company spent an eye-watering $45 billion on automation. But the spending saw its global market share rise by just a single percentage point, to 22 per cent. Over the coming years, it increasingly lost market share, and watched as Toyota delivered low-cost, high-quality vehicles with a low-tech production approach. As a nameless GM exec said at the time: "For the same money we could have bought Toyota and Nissan outright."
1. Foxmeyer, 1996
In 1996, Foxmeyer was the second largest wholesale drug distributor in the US, with sales of more than $5bn. Then it decided to revamp not only its IT systems but also all of its distribution facilities. It was leading-edge stuff at the time - almost in the realms of science-fiction. Accordingly, the company forecast huge efficiency gains from its new systems, and had such confidence in those forecasts that it bid future contracts based on expected cost reductions. Big, big mistake. Its new systems did not deliver any cost savings, because they barely worked, and so it was unable to handle any of its vastly increased orders. Before long, Foxmeyer had filed for bankruptcy, and its operating division was sold to rivals McKesson, for just $80 million.
Digital Magazine
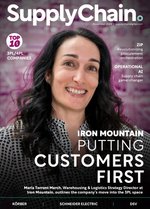
- FedEx: Supporting Healthcare Logistics in Asia-Pacific Logistics
- Maersk and Syngenta: Committed to Responsible Logistics Logistics
- Top 10: Logistics Technologies Transforming the Industry Logistics
- BMW's Move to Sustainable Logistics with Electric Trucks Sustainability
Featured Articles
Blue yonder’s demand planning boost for manufacturers.
Blue Yonder's Cognitive Demand Planning assistant is helping manufacturers to address the complexities of the high-tech manufacturing landscape …
Why Supply Chain Transformation Needs a Process-Led Approach
In this new white paper, Supply Chain Digital, in association with Celonis, examines the importance of understanding supply chain processes …
Webinar: Coupa & Amazon Business on Streamlining Buying
In this upcoming webinar, leaders from Coupa and Amazon Business will shed light on how their partnership provides a streamlined purchasing experience …

Interos: Building Trusted and Transparent Supply Chains
Kinaxis: the 'customers' choice' for supply chain planning, why coupa has been named a supply chain leader by forrester.
- Trick or Treat: Inside the $11.6bn US Halloween Supply Chain
- Why Vanderlande has Agreed to Acquire Siemens Logistics
- Procurement & Supply Chain LIVE: Sustainability – The Agenda
- Maersk & Danone: Partnering Towards Greener Logistics
- KPMG: Proximity the new Value Driver for Supply Chains
The 2025 Top 10 ERP Systems Report
Our experts have highlighted ten vendors that can help your organization make data-driven decisions.
The 2024 ERP Report
Every year, Panorama analyzes industry trends to understand organizations’ selection and implementation practices when it comes to enterprise software.
ERP selection & implementation
Management consulting
Software Expert Witness
The 2024 Top Government ERP Systems Report
This independent report highlights the ERP vendors that Panorama has found to be highly functional for states, municipalities, nonprofits, and other public sector entities.
Reports & Whitepapers
Tools & Resources
Events, Webinars & Podcasts
ERP Consultations
Popular Blogs
Top 10 ERP Software
Our list of top 10 ERP software highlights the vendors our ERP experts have found to be innovative and strong in functionality. This is an overview of those ERP systems.
Blog Collection
Lessons Learned From the Nike Supply Chain Management (SCM) Failure
by Bill Baumann | Jan 27, 2022
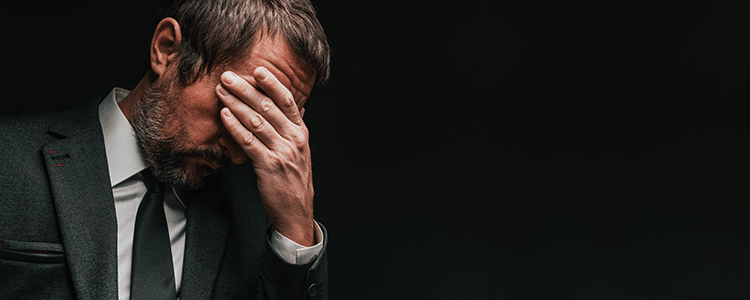
A supply chain management system is supposed to help a company streamline and centrally manage its flow of goods and services. It isn’t supposed to result in excess inventory or lead to extensive order delays.
Yet, that’s exactly what happened when Nike implemented an SCM system back in 2001. Performed in partnership with i2 Technologies, the project started off promising but quickly veered off-track. As a result, the mega-brand’s supply chain malfunctioned at several critical junctures, leading to a significant dip in profits.
Today, we’re taking a closer look at the Nike SCM failure in this inventory management case study . We’ll share what happened, the lessons learned, and how you can avoid a similar fate in your own implementation.
Contemplating litigation?
We have multiple software expert witnesses available for provision of reports, depositions, and testimonies.
The Nike SCM Failure: What Happened?
At its core, SCM software is designed to help companies reduce their operating costs by enabling more accurate and timely forecasts. With the right platform, users can better anticipate their suppliers’ purchasing requirements, as well as upcoming customer orders.
Nike began installing the i2 SCM software in 2001. The goal was to automate certain parts of the supply chain for its footwear division, including inventory and order management.
When the system went live, however, it was unable to match Nike product inventories with customer demand. As a result, the company experienced both excesses and shortages — both of which cut into their bottom line.
In fact, Nike announced that as a result of its failed SCM project, it would be unable to meet its third-quarter projections.
According to one analyst, the financial implications were even greater. Specifically, the SCM breakdown with i2 was only one part of a larger technical failure that ultimately cost Nike $400 million over the course of the year.
The failure also caused i2 stock to drop 22% , and led to a public dispute between Nike and i2.
Let’s look at the phases leading up to this SCM failure and discuss how it could have been avoided.
4 Lessons Learned From The Nike SCM Failure
Are you planning an SCM implementation at your organization? When all the right steps are in place, these platforms have the potential to transform your supply chain operations for the better.
Yet, as evidenced by Nike, the wrong moves can have the opposite effect.
Here are a few key lessons learned:
1. Keep Industry Complexity in Mind
One challenge that Nike faced was an inventory that was both vast and varied.
This is the case with most retail establishments. Trying to organize everything into an SCM system is a complex and time-consuming endeavor. Not only are there different products, but there are also different color options and sizes to consider.
It’s important to make sure you have the time and resources in place to input all this data before going live. This includes allocating the right personnel to the effort.
In this case, Nike hired the i2 consulting team to oversee the transformation, but there were still insufficient protocols to protect against critical software issues.
Considering that this was meant to be a multi-year systems upgrade that would eventually lead to global deployment, project leaders should have built a project plan that accounted for industry-specific challenges.
2. Software Customizations Can Strain a Project
Many times, organizations will choose to customize some functions of their SCM, CRM, or ERP system . While these changes can help the software work for an organization’s unique needs, they can also heap additional cost and risk onto a project.
With the Nike project, representatives acknowledged that standard methodology wasn’t in place during the implementation. While the i2 software came equipped with an apparel industry template, Nike chose not to use it.
Instead, they pursued a custom approach and rushed the migration process, settling for data that insufficiently represented their company. This strained the software beyond its built-in capabilities and led to issues with data transfer.
3. Tests and Pilot Runs are Key
One of the most glaring issues with the Nike SCM implementation was that the system, which affected the brand’s global supply chain, wasn’t tested even once before it went live.
Testing is an essential stage in any enterprise software project. It gives the IT team a chance to identify and remediate any bugs or problems. This ensures fewer headaches when it’s finally time to go live.
At the same time, it’s equally important to conduct system pilot runs. This ensures the software, data, and processes all work together seamlessly.
Going live without adequate testing or conference room pilots not only leaves the system ripe for failure but can also decrease user morale. A platform that malfunctions does little to increase confidence in new workflows, which can lead to organizational change management challenges.
4. The Right Talent Makes a Difference
The people at the helm of an SCM project can greatly influence its success. Both Nike and i2 admitted shortcomings in this regard.
This was a major project that required top-tier talent. Both sides should have been equally invested in the outcome by building a strong project team.
Unfortunately, Nike’s IT staff was already stretched thin at the time of the implementation because employees were focusing on two other projects involving ERP and CRM software .
Optimize Your SCM Implementation
The challenges involved in the Nike SCM failure don’t have to deter you from pursuing a similar project at your own company. As long as the right plans are in place, SCM software or ERP implementation can help you improve the efficiency of your supply chain management processes.
Contact our enterprise software consultants below for a free consultation.
About the author
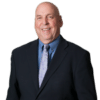
Bill Baumann
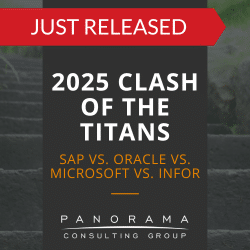
Posts You May Like:
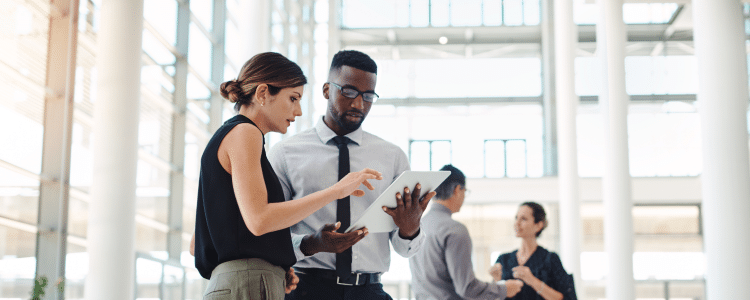
The Hidden Pitfalls of Integrating External Data: Challenges & Advice
In an era where data-driven decision-making defines competitive advantage, integrating external data into ERP systems is a strategic priority for many CEOs. External data can provide critical insights, enhance predictive analytics, and improve customer experiences....
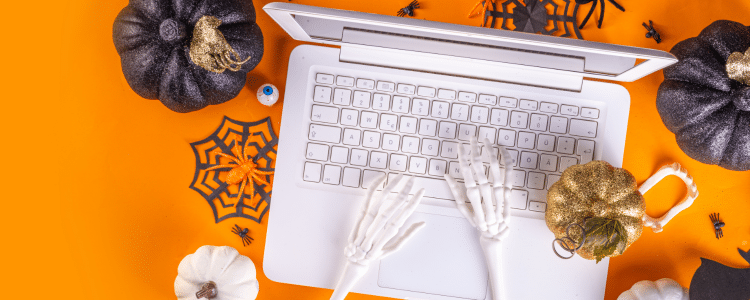
The Scariest User Adoption Challenges in ERP Implementations
Software implementation projects can be exhilarating—an ambitious roadmap, a modern ERP system, promises of streamlined processes, and a more efficient future. But if you've led such a project, you know the real fright isn’t found in the technology itself. Instead,...
Privacy Overview

IMAGES